The all-new LTX Series Twin-Screw Extruders - our latest product for 2023 come with an array of advanced features. These include a larger groove depth ratio, increased length-to-diameter ratio, a high-torque gearbox, higher screw speeds, and dual-screw side feeding. The application of these technologies ensures that materials are thoroughly dispersed and mixed at lower temperatures, thanks to the high-speed rotation of precision intermeshing elements. This enables the LTX Series to meet the requirements of even the most demanding product specifications.
Do/Di Ratio =1.7 for optimum free volume and high production yields.
Up to 18 Nm/cm³, ensuring superior extrusion performance.
Standard 4D liner design, customizable for various length-to-diameter ratios.
Full product line with self-cleaning screw design for long-term use without particle solidification.
Conveying and kneading screw elements configurations to match specific production requirements.
Facilitates machine cleaning and color changes, reducing downtime during production.
Screw elements, liners, and core shafts made of high-quality alloy steel, with custom material options.
Pneumatic-assisted lid opening simplifies access, improving efficiency.
Featuring advanced sensors and automation ensures smooth feed production, maintains product consistency, and eliminates the risks associated with manual intervention.
Hopper equipped with material level detection for better operational control and safety.
Direct cooling waterway design for optimized temperature control during production.
Cooling system with a water tank, pump, and heat exchanger for constant temperature control.
PID-controlled cooling and heating systems for temperature accuracy within ±2°C.
Control over lubrication oil temperature and monitoring of oil pressure for optimal machine performance.
Touch screen and PLC control for a convenient human-machine interface, reducing training costs.
Choose from warm-up, standby, and full production modes to adapt to different production stages.
Software package includes formula management and maintenance tools for easier operation and upkeep.
Comprehensive safety protection system for operator and machine safety.
Customize with optional torque limiters and metal detectors to meet specific production needs.

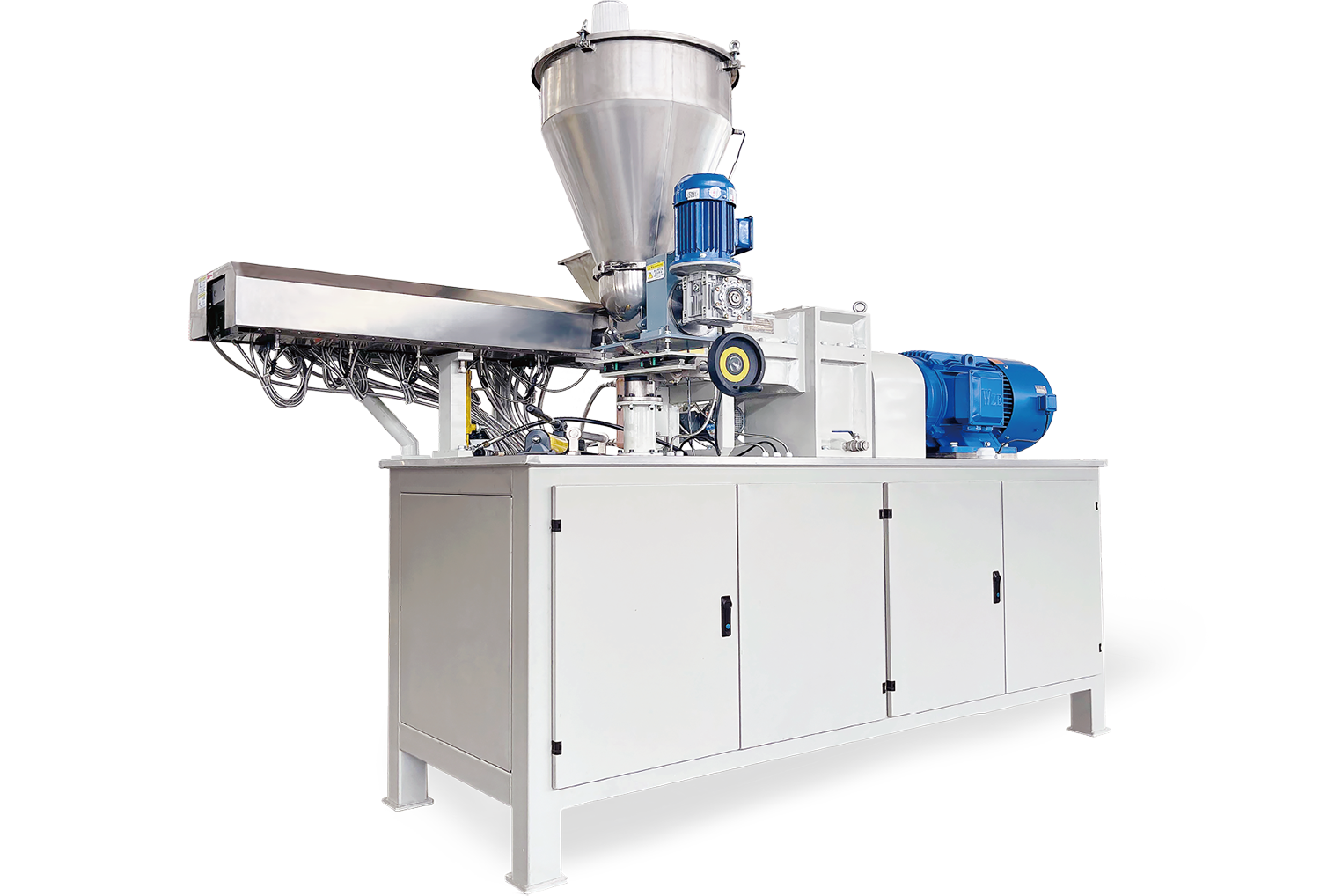
The 16:1 length-to-diameter ratio series is designed for handling textured powders and epoxy powders (fast-reacting type)
Model | Screw diameter | Do/Di | Screw Speed | Motor Power | Max output |
LTX-41-16 | 42.7 | 1.7 | 400-600 | 15-22 | 150-200< |
LTX-50-16 | 52.1 | 1.7 | 400-600 | 22-37 | 200-400< |
LTX-65-16 | 64.6 | 1.7 | 400-600 | 45-75 | 450-800< |
LTX-75-16 | 74.5 | 1.7 | 400-600 | 75-110 | 800-1200< |
LTX-95-16 | 96.9 | 1.7 | 400-600 | 160-250 | 1500-2500< |
The 24:1 length-to-diameter ratio series is ideal for high-gloss and highly dispersed powder coatings.
Model | Screw diameter | Do/Di | Screw Speed | Motor Power | Max output |
LTX-25-24 | 25 | 1.68 | 600-900 | 5.5-9 | 50 |
LTX-32-24 | 32 | 1.68 | 600-900 | 11-22 | 100-200 |
LTX-41-24 | 42.7 | 1.7 | 600-900 | 30-45 | 300-400 |
LTX-50-24 | 52.1 | 1.7 | 600-900 | 55-90 | 600-800 |
LTX-65-24 | 64.6 | 1.7 | 600-900 | 110-160 | 1000-1500 |
LTX-75-24 | 74.5 | 1.7 | 500-750 | 135-250 | 1400-2500 |
The 48:1 length-to-diameter ratio series is tailored for acrylic powder coatings.
Model | Screw diameter | Do/Di | Screw Speed | Motor Power | Max output |
LTX-32-48 | 32 | 1.68 | 800-1200 | 30-45 | 150 |
LTX-41-48 | 42.7 | 1.7 | 800-1200 | 75-110 | 400 |
LTX-50-48 | 52.1 | 1.7 | 800-1200 | 132-200 | 800 |
LTX-65-24 | 64.6 | 1.7 | 800-1200 | 200-350 | 1500 |

Automatic Weighing System
Automated control, precise weighing
Automated carton recognition, fills in pre-set amount for the carton size
Vacuum system recycles escaping powder, minimising contamination
Only 1 operator needed, lowered production cost, high production efficiency
Lengths: 2m, 2.5m, 3m for your practical needs